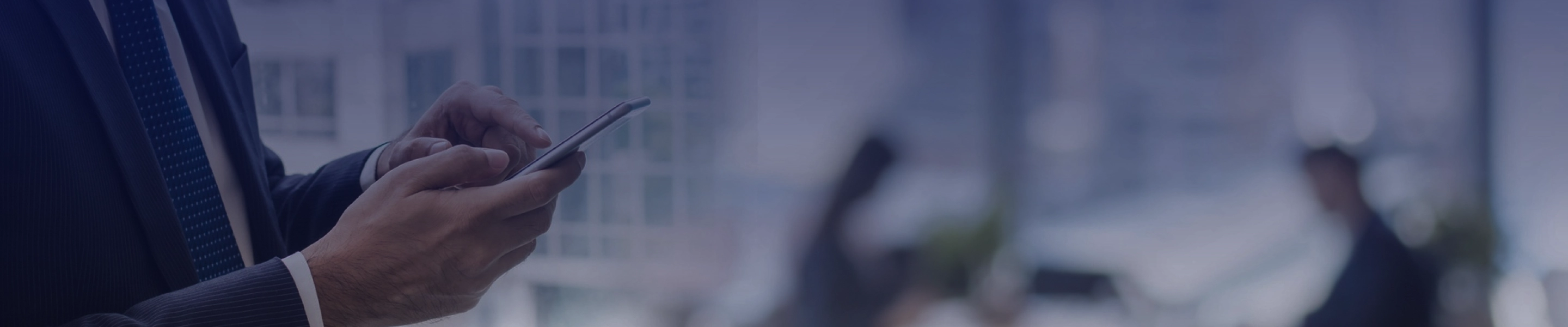
Investor FAQ
To provide an estimate, let's consider the figures from our Sakon Nakhon factory, since its cost structure is independent from the central expenses of the group. Our calculations indicate that the breakeven point is reached at about 60% of the total production capacity.
For the majority of our customers, who are international clients, once the company receives a product order, the delivery typically occurs within a 3-month period from the order date. Therefore, it can be said that the company is aware of orders roughly within the same timeframe.
The company has implemented the following strategies:
- Establish a strong network of farmers near our factories to engage them, leading to farmers selling their products to our company.
- Educate farmers by advising on cultivation methods and recommending crop varieties that yield high-quality produce with a high percentage of starch and disease resistance.
- Set up a dedicated team to support our partner farmers, promptly addressing their problems and finding immediate solutions.
- Utilize a network of middlemen who can collect cassava from various sources and sell it to our company.
- Increase the production capacity of our factories to handle large volumes during peak seasons. This helps to compensate for lower production during the low season. Historically, the cassava harvest peaks from January to March and again from August to October.
Additionally, the company is expanding into the modified cassava flour business to add value to our existing cassava products. This modified cassava flour has a higher profit margin and helps offset the reduced profits from standard cassava flour during low production periods.
The planned gross profit margin is around 20% (The gross profit margin for the years 2021-2022, which was approximately 25% and 22% respectively, represents the normal rate for our business). Currently, thanks to successful cost management strategies, particularly in electricity expenses, the company has been able to reduce costs significantly. This is largely due to owning our own power generation facilities, which has greatly aided in reducing electricity costs.
- The company is committed to managing its selling and administrative expenses to not exceed 10% of total revenue. Currently, we have approximately 521 employees across our network. With the construction of our new factory, there's a planned integration of technological advancements in machinery, which is expected to reduce the workforce.
- Presently, the company operates two cassava flour production plants (located in Mukdahan and Sakon Nakhon) and one power plant.
- Modified starch is a form of tapioca starch that has been enhanced with additional properties as per individual customer agreements. Customers use modified starch in various products, making it a made-to-order item. This customization allows for higher profit margins compared to regular tapioca starch.
- Our company produces modified starch in two forms:
- We own certain formulas, which are mostly semi-finished products well-known within specific industries and are ready for immediate sale.
- We also develop unique formulas in collaboration with clients, involving specific agreements and long-term contracts with each client.
For our modified starch products, in the initial phase, the company plans to enter the market in areas where we have marketing expertise, starting with China. Subsequently, we will expand to other countries. Initially, we will focus on customers in the paper and food industries.
Let's take the example of a new cassava flour production factory in Kalasin Province. The company plans to employ approximately 130-140 people, including both salaried and daily-wage workers. The daily-wage workers will be divided into three shifts. The increase in the number of employees will depend on the integration of technology into the production process.
In our manufacturing process, we utilize automation systems starting from the conveyance of raw materials to the washing pits, chopping and grinding of cassava roots, extraction and separation of water from starch, drying processes, all the way to the packaging stage.
With our extensive expertise and long-standing experience in business operations, coupled with our robust financial strength, our company is well-equipped to expand our investments to other areas. This is exemplified by our ongoing project of establishing a new factory in Kalasin Province.
Furthermore, in the context of the volatile raw materials market and intense competition in the procurement of cassava, some local operators who struggle with adapting, face capital shortages, or lack systematic management, decide to exit the business. In such scenarios, our company remains open to exploring the feasibility of acquiring assets or businesses from these operators.
The company anticipates significant and continuous growth in both revenue and profit over the next five years. In the short term, this growth is expected to stem from the operations of the company's two new factories: a tapioca flour factory in Kalasin Province and a modified tapioca flour factory, which will begin production and start generating revenue from the second quarter of 2024. The revenue is expected to increase gradually with the utilization of production capacity. Additionally, for the existing factories in Mukdahan and Sakon Nakhon, the company plans to invest in enhancing operational efficiency, which will also improve the ratio of revenue to cost.
In the long term, the company is exploring growth opportunities through expanding production capacity in suitable areas. This could involve self-invested expansions in new plants, similar to the Kalasin factory, or acquisitions of other tapioca flour manufacturing businesses or assets.
The year 2023 posed various challenges for our business operations in this industry, starting from the beginning of the year. We faced a severe flood situation in the Northeastern region, leading to rotten cassava issues and a shortage of planting materials for farmers. This was followed by a drought, stunting cassava growth, and leading to diseases like mosaic virus, whiteflies, and mealybugs, significantly reducing the quantity and quality of cassava in the market, thereby impacting the starch production industry.
Our company operations were also impacted, without exception. Our management team endeavored to mitigate these impacts through various measures, such as collaborating with partners to source scarce cassava, supporting farmers with planting materials, and implementing incentive measures beyond purchasing prices. Additionally, the strong demand for our products from key customers enabled us to maintain high sales prices, ensuring that, despite not meeting expected targets, we still achieved continuous profit in a year where many in the industry faced losses.
The best decision made over the past year was to move forward with our initial public offering (IPO) early in the year. This strategic move reduced our financial costs and provided sufficient capital for business expansion, including in our Modified Starch plant. This expansion not only helps maintain our profit margin but also elevates the company's reputation to a new level. We are now able to produce higher-technology products, distinguishing our company from the numerous other cassava producers in Thailand.
Throughout our operation since 2005, our company has been recognized as a manufacturer with expertise in producing Tapioca starch. Our products are of high quality, meet standards, and are accepted by customers both domestically and internationally. We have received various quality standard certifications, including ISO9001:2015 for Quality Management System, ISO14001:2015 for Environmental Management System, and certifications from the United Kingdom Accreditation Service, which is internationally recognized, demonstrating fairness and operational and management standards of international quality.
Our company also meets the HACCP (Hazard Analysis Critical Control Point) standards for food and drug safety, GMP (Good Manufacturing Practice) for quality food production practices, Halal standards for products that comply with Islamic laws, and green industry standards.
Furthermore, to produce products that meet customer needs with quality and universally accepted standards, our company has defined the following marketing strategies:
- Differentiation strategy in products, such as producing premium-grade Tapioca starch.
- Strategy to find new customers and increase sales for existing customers.
- Strategy to sell Tapioca starch focusing on fast and timely service.
- Strategy to continually improve product quality and production efficiency.
- Strategy to satisfy customers in terms of quality and service.
- Strategy to build business partnerships to create competitive advantages.
The company expects to be able to control the construction project costs for the new Tapioca starch production plant in Kalasin province and the modified Tapioca starch production plant in Mukdahan province within the set budget. In 2024, it is anticipated that the factories will begin operations for the first year, and the company will recognize an increase in depreciation expenses from both projects, estimated at about 6 to 6.5 million baht per month.
In the first two months of 2024, the volume of cassava entering the market increased seasonally compared to 4Q23, allowing the company to manage the cost of purchasing cassava efficiently and maintain a good rate of production capacity utilization. Additionally, the average selling price has remained high due to strong customer demand for the product. Consequently, the company expects that the spread between the cost of raw materials and the selling price will slightly improve in 1Q24 compared to 4Q23.
The Northeast region is a significant cassava planting area in Thailand, accounting for more than 54% of the country's cassava cultivation area. The locations of our company's factories, which are in Mukdahan, Sakon Nakhon, and Kalasin provinces, as well as the surrounding areas, are considered regions where cassava is widely cultivated and have suitable raw material availability.
The purchase prices for cassava raw material vary according to the percentage of starch content measured randomly from the cassava when farmers bring their produce for sale. Generally, the average starch content percentage measured from purchases is about 25%. Therefore, it can be said that the purchase prices for cassava raw material at the 25% starch content level more accurately reflect the cost of cassava raw materials.
In years when cassava production is normal and not adversely affected by changes in weather conditions or natural disasters, the utilization of the existing factory's production capacity is considered to be at a high level, such as in 2021-2022, where the seasonal capacity utilization was between 72% and 83%. Therefore, to support future growth, the company sees the importance and necessity of planning additional production capacity expansions. Expanding production capacity into new geographical areas will help diversify the raw material procurement areas, reduce the risk of natural disasters or epidemics which often have localized effects, and simultaneously improve the efficiency of cost management.
The cassava mosaic virus outbreak started severely for the first time in 2018, spreading through diseased cuttings and whitefly vectors. Although in 2021, the cabinet approved a budget of over 1,300 million baht for compensating farmers who destroyed diseased plants and for other measures to address the issue, and in 2022, the government claimed success in controlling the cassava mosaic virus as announced by the Department of Agricultural Extension, the reality is that the outbreak situation still persists.
However, efforts to prevent and curb the spread of the cassava mosaic virus from spreading to other areas continue. Relevant agencies, such as the tripartite private sector committee (Joint Private Sector Committee), have implemented various measures, such as the control of moving in or out of areas affected by the outbreak, covering most of the planting areas in the Northeastern region, for example.
Even in the company's operating areas, where the outbreak situation may not be as severe as in other areas, the company recognizes the risk that farmers may face a shortage of planting material after the price of cassava cuttings increased in some areas. The company is aware and prepared to deal with this, such as investing in research and development in collaboration with external agencies and setting up trial areas to obtain disease-resistant cassava varieties for promotion and support of farming activities for affected farmers.